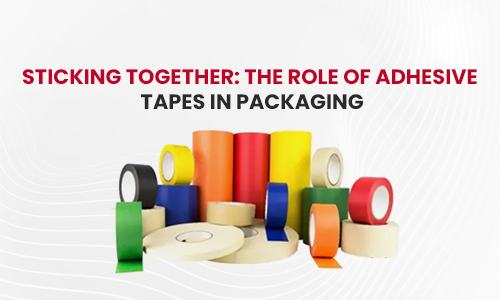
Why do we need tapes in our lives?
Adhesive Tapes are also known as sticky tapes that can fix things, hold stuff together. Glue, fabric, animal skins, and strings were used to bind things together when tape was not invented. Once tape came into our lives, the first thing that came in mind of people to fix things was “Tapes”.
In olden days to pack a product string or twine, is used. The process was very time consuming and not perfectly packed. Adhesive Tapes made the process fast and efficient leading to fast packaging, shipping and cost effectiveness.
And that's not all, adhesive tape also plays a crucial role in keeping wounds together, helping with medical care. Nowadays, Adhesive tapes come with different sizes and different adhesive strength(stickiness). They can be gentle to super sticky with more versatility and can be used practically anywhere to bind a product. Adhesive Tapes are used in a variety of industries, in household, in packaging, shipping, construction, decoration, in medical, office, and also safety purposes. Thus Tapes became an integral part of our daily life. Whenever something is broken, the first thing we think of is to fix it by taping it or gluing it. But using Tape is more convenient.
What is the history of tapes?
Below is the table the timeline and details in the history of adhesives and tapes:
Year |
Innovation |
Details |
617-906 A.D. |
Chinese Adhesives |
Made from fish, ox, and stag horns. |
1750 |
First Adhesive Patent |
Issued in Britain for a fish-based glue, leading to the first commercial glue plant in Holland. |
1845 |
Invention of Surgical Tape by Dr. Horace Day |
The first tape was made from cotton for medical use, primarily for bandaging. |
1845 |
Paper-based Adhesive Tape by Richard Wolffenstein |
Invented a paper-based adhesive tape using gelatin. |
1890s |
Cellulose-based Tape |
Developed from nitrocellulose, offering improved adhesion for sealing envelopes. |
1921 |
Invention of the Band-Aid by Earle Dickson |
Created at Johnson & Johnson to keep dressings on small wounds. |
1925 |
Pressure-sensitive Tape by Richard Drew |
At 3M, combining rubber with adhesive for a stronger, more versatile product. |
1930 |
Masking Tape |
Developed by Richard Drew for painters to achieve clean lines without damaging surfaces. |
1946 |
Filament Tape |
Patented by Cyrus W. Bemmels, fiberglass filaments are used to strengthen for increased strength. |
1970s |
Velcro Tape |
first released as a reusable fastening method made up of hook and loop elements. |
1980s |
Double-sided Tape |
which has adhesive on both sides for bonding two surfaces—becomes widely used. |
1990s |
Foam Tapes |
used with single- or double-sided adhesive for gasketing, sealing, and insulation. |
2000s |
Nano-tape |
utilizing nanotechnology in consumer and industrial applications to provide robust, residue-free adherence. |
How are Tapes manufactured?
The steps below are involved in the manufacture of tape:
- Starting with a tape material (substrate), determine which side of the material (substrate) will contain the adhesive.
- On the material's adhesive side (substrate), apply a primer.
- On the worktable, apply thin layer rubber-based adhesive. any extra liquid that is extra can be removed by heating it, application of hot air to it, or by laminating with high pressure. This process completely depends on the type of adhesive tape. This process guarantees that the adhesive is good to use, with no impurities.
- To make it easier for users, coil the tape onto a cardboard roll at the end. The end of the tape is frequently kept accessible with the help of certain ingenious solutions that add an edge separator—which could be made of colored paper.
Why are tapes sticky?
The fundamental component required to create the basis of adhesive tapes is adhesive. Adhesives are that give materials (substrate) their stickiness. These adhesives can be formed of rubber, acrylic, silicon, epoxy resins, synthetic rubber, polyurethane, solvent-based adhesives, or acrylic-based adhesives.
Here's a table summarizing the pros and cons of different types of adhesives:
Type of Adhesive |
Pros |
Cons |
Rubber |
Less expensive |
Prone to oxidation |
High initial tack |
Limited at higher temperatures |
|
Adheres well to various surfaces |
Susceptible to UV light |
|
Acrylic |
Stable to oxidation and UV light |
More expensive than rubber/resin |
Long-lasting protection against UV light |
Not as effective on hard-to-adhere surfaces |
|
Silicone |
Long service life |
The most expensive |
High flexibility |
||
Resistant to high temperatures |
||
Epoxy Resins |
High strength and low shrinkage |
Not as flexible |
Tough and resistant to chemicals |
||
Synthetic Rubber |
High adhesion and shear resistance |
More expensive than natural rubber-based |
Suitable for sealing packages and cartons |
adhesives |
|
Polyurethane |
Provides flexibility, impact resistance, |
Generally more expensive |
Isocyanate |
and durability |
Generally more expensive |
Features of Acrylic Tapes and Solvent Tapes?
When choosing acrylic tape and solvent tape, the foremost question will be which one is better suited for our product.
Below is the table explaining the features of acrylic tapes vs solvent tapes:
Feature |
Acrylic Tape |
Solvent Tape |
Weather Resistance |
Excellent; UV resistant, good for outdoor use |
Varies; some types may degrade under UV light |
Longevity |
Maintains adhesion and appearance over time; does not yellow |
May weaken under extreme temperatures; potential yellowing over time |
Environmental Impact |
More environmentally friendly with fewer VOCs |
Emits more VOCs; potential health and environmental concerns |
Adhesion to Surfaces |
Good on a variety of materials, including plastics and metals |
Strong on diverse surfaces; might have issues with specific materials |
Clarity |
Remains clear over time |
Can vary; some types may yellow with UV exposure |
Initial Tack |
Strong but may take time to reach full strength |
Very strong and immediate |
Temperature Sensitivity (Application) |
Less effective in cold conditions during application |
Performs well in a broader range of temperatures during application |
Chemical Resistance |
Less resistant to certain chemicals and solvents |
Better resistance to chemicals and solvents |
Cost |
Generally more cost-effective |
Typically more expensive |
This table provides a quick comparison, but the choice between acrylic and solvent tape should be based on the specific needs of the application, including environmental conditions, bonding surfaces, and any health or environmental concerns.
What are the usual layers and components of sticky tape, and how is tape-dispensing process waste reduced and made simpler?
In general, adhesive tape consists of up to two or three layers. Various materials (substrate) such plastic, foam, cloth, foil, even paper can be applied to create the initial layer. The adhesive, which can be built of polymers like silicone, isocyanate, acrylics, epoxy, rubber, or polyurethane, makes up the second layer. The release liners, which frequently consist of paper, is the third layer, which may or may not be present. It protects the adhesive until it is removed and discarded away once the tape is dispensed. Release agents should not transfer into the adhesive. They should ensure consistent release and unwinding. Moreover, these agents must preserve their properties and stability over time, even in diverse climatic conditions. Some tapes also have an edge separator at the outer side of the tape roll which is made of colored paper to stop the edge of the tape from sticking to the roll.
Tapes are commonly supplied in circular roll form for easy dispensing. There are various tape dispensers available in the market that simplify the tape dispensing process and reduce tape waste. This is particularly important as dispensed tape can sometimes stick to itself rather than the intended surface so use of dispenser helps to reduce wastage.
What advantages does tape have over glue?
Advantages of Tapes Over Glue |
Explanation |
Cleaner and Less Messy |
Tapes provide a mess-free application. |
Immediate Bonding |
Tapes bond instantly without drying time. |
Consistent and Uniform |
Tapes offer a uniform thickness of adhesive. |
Easily Automated |
Tapes can be automated for efficient assembly. |
Bonds to Various Surfaces |
Tapes adhere to a wide range of materials. |
Weather and UV-Resistant |
Tapes resist weather and UV exposure. |
Clean Application |
Tapes can be applied cleanly, unlike glue. |
Precision and Control |
Tapes allow precise and controlled placement. |
Repositioning Flexibility |
Some tapes permit repositioning before bonding becomes permanent. |
No clamps or Extra Tools Required |
Tapes typically don't need clamps or additional tools. |
Moisture and Humidity Resistance |
Many tapes are resistant to moisture. |
High Durability in Challenging Conditions |
Tapes provide strong bonds, especially in challenging environments. |
Which kinds of tapes are available based on their composition?
There are several tape categories as listed down below, each with a distinct description to prevent any two categories from being repeated:
- Acrylic Tapes: Acrylic compounds are used to make adhesive, which is used in acrylic tape and comes in solvent- or water-based forms. Solvent based acrylic adhesive tapes have strong bonding and it is resistant to chemicals and adverse temperatures. While water based acrylic adhesive tapes are cheaper as well as environmentally friendly than solvent based acrylic tapes.
- Solvent Tapes: Solvent tape is made of adhesive that is made of synthetic polymers which are dissolved in organic solvents. It gives very strong adhesion and durability, although it is more costly and less environmentally friendly compared to water-based alternatives.
- Non-adhesive Tapes: Non-adhesive tapes do not need any kind of adhesive, as they are self adhering. Some of the examples would be stretch wraps, protective films, hook and loop, PTFE thread sealing tapes.
- Heat-Activated Tapes: Heat-activated tape employs a thermoplastic adhesive that becomes adhesive when exposed to heat. Heat activated tapes are mainly used for binding fabrics, metals and plastics.
- Water-Activated Tapes (Gummed Paper Tape): Water-activated tape is made of a starch-based adhesive applied on a kraft paper backing. Water activated tapes when moistened become sticky and ready to use. It is mostly used in packaging for security. Tamper evident tape is a classic example of water activated tapes.
- Reinforced Gummed Tapes (RGT): Reinforced gummed has a backing of two layers of paper and laminated fiberglass filaments. It is a special form of water-activated tape. It is strong, durable.
What is the tape chemistry, characteristics and uses of different packaging tapes?
Below is the table for different types of tapes with its chemistry, characteristics and uses:
Tape Type |
Tape Chemistry |
Characteristics and Uses |
Masking Tape |
Paper and adhesive |
Used for masking off areas during painting and crafting |
Filament Tape |
Fiberglass-reinforced backing and adhesive |
Provides strength for bundling and packaging |
PVC Tape |
Polyvinyl chloride (PVC) backing and adhesive |
Resistant to moisture, used for electrical insulation |
Copper Tape |
Copper backing with adhesive |
Used in electronics and for electromagnetic shielding |
Water Activated Tape |
Kraft paper backing with starch-based adhesive |
Used for secure packaging with tamper-evident seal |
Duct Tape |
Polyethylene backing with rubber adhesive |
Known for its versatility in repairs and sealing |
Heat Activated Tape |
Thermoplastic adhesive activated by heat |
Bonds various materials under heat and pressure |
Double Sided Tape |
Adhesive on both sides of a backing material |
Used for mounting, bonding, and attaching items |
Foam Tape |
Foam backing with adhesive |
Provides cushioning and insulation in various applications |
Paper Tape |
Paper backing with adhesive |
Commonly used for sealing and packaging |
Cloth Tapes |
Cloth backing with adhesive |
Offers durability and flexibility for repairs and binding |
Printed Tapes |
Various backings with printed designs |
Used for labeling, branding, and decorative purposes |
Pressure Sensitive Tapes |
Adhesive-coated backing material |
Bonds upon application of pressure, versatile use |
Non Adhesive Tapes |
Self-adhering tapes without traditional adhesives |
Includes protective films, stretch wraps, etc. |
Tamper Evident Tapes |
Designed to show evidence of tampering |
Used for security and sealing sensitive packages |
Strapping Tape |
Reinforced backing with adhesive |
Provides strength for bundling and securing items |
Stretchable Tapes |
Stretchable materials with adhesive |
Used for wrapping and securing irregular shapes |
Nano Tapes |
May refer to tapes using nanotechnology |
Potential uses in advanced applications |
Flatback Paper Tapes |
Flatback paper backing with adhesive |
Used for splicing, sealing, and packaging |
Safety Tapes |
High-visibility colors and adhesive |
Marking hazards and enhancing safety in various settings |
PVC Foam Tapes |
PVC foam backing with adhesive |
Offers cushioning and sealing properties |
Anti-Slip Tapes |
Textured surface for grip and adhesive |
Used to prevent slipping on stairs and surfaces |
Reflective Tapes |
Reflective material with adhesive |
Enhances visibility in low-light conditions |
Various backings with adhesive |
Primary tape for sealing and securing packages |
|
Adhesive Transfer Tape |
Adhesive layer on a release liner |
Used for bonding and mounting applications |
Security Tape |
Designed for tamper evidence |
Used for sealing and securing sensitive items |
Label Protection Tape |
Clear or translucent backing with adhesive |
Protects labels and markings on packages |
Poly Strapping Tape |
Polypropylene backing with adhesive |
Provides strength for bundling and securing items |
Carrying Handle Tape |
Reinforced backing with handle cutouts |
Facilitates carrying of packaged items |
Office Tape |
General-purpose tape for office use |
Commonly used for everyday tasks and office needs |
Surface Protection Tape |
Protective film with adhesive |
Shields surfaces from damage during construction and painting |
Invisible Tape |
Clear backing with adhesive |
Virtually disappears when applied, ideal for documents |
Mounting Tape |
Double-sided adhesive for mounting items |
Used for mounting photos, artwork, and decorations |
Cellophane Tape |
Cellulose backing with adhesive |
Transparent tape used for various household tasks |
Hook and Loop Tape (VHB Tape) |
Two interlocking fabric strips |
Offers resealable and repositionable fastening |
Glue Dot Tape |
Double-sided adhesive dots on a backing |
Provides quick and mess-free bonding in various crafts |
Flagging Tape |
Non-adhesive colored tape |
Used for marking and flagging purposes in various industries |
Decorative Tape |
Various designs and colors on backing with adhesive |
Adds decorative elements to crafts and projects |
Magnetic Tape |
Magnetic backing with adhesive |
Ideal for magnetic displays, closures, and attachments |
Copper Tape |
Copper backing with adhesive |
Used in electronics and for electromagnetic shielding |
Under what circumstances do packaging tapes can't perform well?
- Temperature: Regular tapes do not work in cold temperatures, therefore special tapes are made which have higher adhesion quality even in cold temperatures. Temperature sensitive tapes are also called “Cold Temperature Tapes”. They can be used at temperatures lower than 15°C.
- Surface of the product: A clean and smooth surface of the product gives best results in sticking the tape to the product. A product that has dirt, debris, moisture, or grease needs to be cleaned and made free from contaminants before using the tape so a strong bond is created between the tape and product.
- Type of product: Composition of the product also determines which tape needs to be used. Different tapes are used based on what the product is made of metal, wood, plastic or box, painted, laminated or non coated. Failing in selecting and using right tape according to the type of product can lead to weaker bond between tape and product.
- Uniformity: It’s important that the product surface is uniform and flat instead of uneven and rough. If the product is rough and uneven the adhesive tape is difficult to stick to its surface. At one point adhesive tape might stick but would definitely not create a strong bond. That concludes the application area is crucial in choosing the right tape.
- Moisture: The presence of moisture after tape application can expose the product. Depending on the application, various tapes are available in the market, including drywall tape, anti-slip tape, gaffer tape, flex tape, duct tape, and waterproof tape.
- Application of the tape: Application of the tape has to be done properly. A strong bond is formed between the product and the tape when the binding product has seams taped from one end to the other end of the product. If the seams of the product require multiple use of the tape it should be done.
- Aging of the tape: The use of old tapes for sealing products or storing sealed tape products for extended periods can result in tape failure. The tape will change the color from clear to yellow when it ages.
- UV radiation exposure: Sunlight is another cause of tape failure if tape is exposed to sunlight for longer periods of time. Exposure to sunlight(UV radiation) will make tape brittle and eventually break the tape seal.
How to assess tape suitability for your product and key considerations for your purchase decision?
To determine if a tape is suitable for your product, consider the following factors:
- What is the composition and characteristics of your product?
- Is the tape durable, versatile, portable, and flexible enough for your needs?
- How easy is tape in applicability?
- Make sure if dangerous goods are transported the tape used is UN certified.
- Will the product be stored for an extended period or subjected to transit?
- What is the intended use of the tape?
- Is the tape compatible with your product?
- What type of surface does your product have?
- Seek expert advice from the packaging company regarding the best tape for your product.
- Consider ordering a sample for testing.
- Determine whether the tape is needed for short-term or long-term use.
- Assess if tamper-evident tape is necessary for product safety.
- Review the available lab report for the tape's performance and quality.
- Is it environmentally friendly, if that's a concern?
- Will the tape be used for applications like taping displays, cold temperatures, moisture, UV exposure, heat and pressure, painting, crafting, bundling, decorating, strapping, insulating, shielding, tamper-evident sealing, repairing, mounting, cushioning, packaging, protecting, security, wrapping, splicing, safety, anti-slip properties, visibility, markings, carrying, virtually disappearing, shielding, flagging, or electromagnetic shielding?
- Whether the tapes are approved by the Pressure Sensitive Tape Council (PSTC), the American Society of Testing and Materials (ASTM), and the International Safe Transit Association (ISTA)?
Considering these factors will help you select the right tape for your specific product and application.
What kind of tape test is best for your product?
Tensile strength of the tape:
Tensile strength of the tape is the measure of the force required to break a piece of tape by pulling it in opposite directions. This test helps determine the tape’s ability to withstand tension, and the result is observed when the tape breaks. Masking tape or painter’s tape has lower tensile strength than acrylic tape or duct tape.
Peel test or Adhesion test of the tape:
Peel strength of the tape is the measure of the force required to separate a piece of tape from the material (substrate) it is adhered to. The force applied to remove tape from the substrate should be at constant speed and perpendicular in direction to the substrate. If the tape peels off easily from the substrate has weaker strength and if tape takes more strength to remove from the substrate it has stronger strength. There are various test methods used to measure the load per unit width of the tape required to separate from the subtract. The most common method of testing is done by measuring the amount of force needed to peel off the tape from the surface of the substrate at both 90° and 180° angles. This load per unit width is an important factor in assessing the tape’s adhesive strength and performance. Painter’s tape has lower adhesion than acrylic tape or duct tape.
Tack test of the tape:
Tack strength of the tape is the measure of how strongly the tape adheres to the surface of a material (substrate) when minimal pressure is applied during initial contact. The tack test is commonly performed using the rolling ball method, where a metal ball or marble is rolled on the adhesive side of the tape. If the ball rolls a longer distance, it indicates lower tack strength, while a shorter distance suggests higher tack strength of the tape. Painter’s tape is intentionally manufactured with low tack properties, making it easy to remove without leaving behind any residue or causing damage to the surface it was applied to. In contrast, duct tape is designed with high tack properties, allowing it to adhere effectively to a wide range of surfaces and create a strong bond. Duct tape is known for its durability and ability to withstand harsh conditions, including moisture, heat, and cold. It was originally invented during World War II for the purpose of sealing military equipment.
Holding test of the tape:
Holding strength of the tape is the measure of how long the tape can hold a product without sliding it off or breaking off because of the weight. During the test, the distance of displacement is also measured with time as a variable, indicating how long the tape took to slide the product at every point of breakage. Holding strength measures the adhesive strength of the tape. A small strip of tape is hung vertically to a metal board and a weight is hung at the loose end. The time taken by the tape for displacement, either by breaking or peeling, is measured. This determines the holding power of the tape. This experiment can be easily understood by using two different types of tapes to measure the holding power. Masking tape or painter’s tape has lower holding power than duct tape.
Stretch test of the tape:
The stretch test of the tape is measured by how much the tape stretches before it breaks when pulled from both ends. The tape that breaks easily when pulled from opposite ends of the tape is considered weak and has low stretch strength, whereas the tape that does not break easily after stretching from both opposite ends of the tape has stronger stretch strength. It is calculated by dividing the change in length of the tape by the original length of the tape.
Let’s compare the stretching capabilities (strength) of different types of tapes in sequential order from weakest to strongest in below table:
Tape Type |
Stretch Capability |
---|---|
Washi Tape |
5% of original length |
Masking Tape |
10% of original length |
Painter's Tape |
15% of original length |
Scotch Tape |
20% of original length |
Duct Tape |
25% of original length |
From the above table we can say that the Duct tape has the highest stretching capability and also strongest compared to all other tapes.
Shear test of the tape:
Shear strength of the tape is the measure of how well an adhesive can withstand shear stress, which is the force applied parallel to the surface of the material (substrate). This test evaluates the adhesive’s ability to resist slipping or sliding either vertically (up and down) or horizontally (side to side) when subjected to these shear forces. It is a measure of the adhesive’s strength in maintaining its bond under shear stress. In simpler terms, shear stress occurs when two materials (substrate) slide past each other, and the shear test helps determine how well the adhesive can prevent this sliding or separation. It is crucial in applications where the bonded materials (substrate) are exposed to forces that might cause them to shift or move in a lateral or sliding manner. This test provides valuable information about the adhesive’s performance in real-world scenarios where shear forces may be present. The use of double-sided tape to stick two materials (substrate) and check the shear strength by pulling both materials (substrate) in opposite directions until it breaks.
Which organizations set packaging tape standards?
Packaging tape goes through various evaluations and quality checking by organizations like the Pressure Sensitive Tape Council (PSTC), the American Society of Testing and Materials (ASTM), and the International Safe Transit Association (ISTA). These organizations play an important role in making sure that packaging tapes meet the required standards before they are sold in the market.
Packaging tapes are battery tested and assess various aspects of tape performance. These tests include measuring the ability tape has to withstand weight, how strong the tape is during transit, and how long it can maintain its adhesive strength. And also how good the packaging tape is sustainable in different environmental conditions is measured.
While transporting dangerous goods, packaging tapes go through a more stringent testing process. The UN has approved clear guidelines for packaging tapes for safety purposes when it comes to transporting hazardous materials for safety.
Thus these guidelines by the above organizations can guarantee good quality of packaging tapes.
What is the weight-bearing capacity of different mil packaging tapes?
The weight-bearing capacity of various mil tapes varies based on their thickness. As a rough guide, the table below provides estimated weight ranges that different mil tapes can typically seal. It's important to know the general guidelines, specifications and recommendations of the tape manufacturer or supplier so the right tape is selected for your product that needs to be sealed by the tape.
Tape Thickness |
Weight-Bearing Capacity |
2 mil |
Up to 30 lbs |
2.2 mil |
Up to 40 lbs |
2.5 mil |
Up to 50 lbs |
2.9 mil |
Over 50 lbs |
3 mil |
Up to 55 lbs |
3.2 mil |
Over 60 lbs |
4 mil |
Over 55 lbs |
Which styles of packaging tape are used to seal corrugated boxes?
The corrugated boxes are sealed in two styles: H style and U style.
H style: 3 tape strips are used to seal horizontally and vertically the seams of the box.
U style: 1 tape strip is used to seal the only one seam of the box.