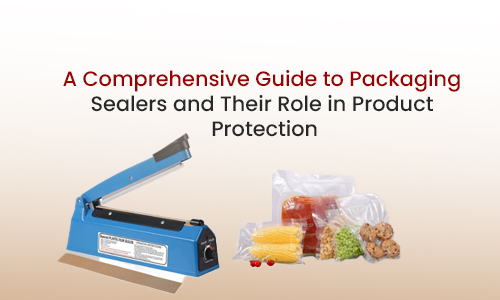
Packaging Sealers and Their Role in Product Protection
To put it simply, when we talk about a "seal" in the context of sealers, we're referring to the barrier created by these sealers. This barrier ensures that things like air, water or other things can't pass through where two surfaces or objects are joined. So, a "seal" is essentially the protective layer formed by sealers to keep things tightly closed and prevent leaks or contamination. Imagine you have two things you want to stick together so that they don't fall apart and nothing like air or water can get through the middle. That's where sealers come in. Sealers are like special glues or materials that help join these two things tightly. They work by creating a barrier that blocks anything from passing through. So, when we use a sealer, we're making sure things stay together and stay protected from things like water or air leaking in or out. It's like putting a cap on a bottle to keep the liquid inside from spilling out.
Sealing technology is essential in the packaging world, playing a key role in keeping products safe, maintaining their quality, and ensuring they look good. It's the foundation of effective production lines, influencing not just the quality and efficiency of the product, but also how the brand is perceived. Companies aim to find sealing solutions that are both cost-effective and reliable, providing secure, durable packaging. Efficient sealing reduces waste during storage and transportation. For non-consumable items, a good seal minimizes damage during transit. For consumable goods, a strong seal not only extends their shelf life but also keeps them fresh, further reducing the chances of loss while in transit.
In the packaging sector, a wide range of sealing machines are utilized, chosen based on the type of material that requires sealing and the specific product that requires sealing.
Let's explore the most common questions and considerations when choosing the right sealer for your product, ensuring that your packaging remains not only secure but also efficient and cost-effective.
What types of materials are suitable for sealers, and is it possible to use sealer to seal boxes?
Sealers are adaptable to a broad range of materials, such as plastics, aluminum foils, glass, and specific paper varieties. Their compatibility largely relies on the design of the sealer and the distinct sealing technology deployed. For instance, heat sealers are typically utilized for sealing plastic bags and pouches, whereas induction sealers are favored for affixing lids to glass jars and bottles.
In the case of sealing boxes, the method varies depending on the material of the box. For example, cardboard boxes are usually not sealed using machines intended for pouches or containers. Instead, boxes are more often sealed using adhesive tapes or glue. Nevertheless, boxes that have a foil or plastic inner lining might be sealed with specialized sealers to enhance product protection or maintain freshness. Therefore, although the direct use of most sealing machines on conventional boxes is rare, sealers can indeed play a crucial role in the packaging process of boxed products by securing internal liners or elements.
In the packaging sector, sealers are compatible with materials including:
- Various Polyethylene types, such as HDPE, LLDPE, and standard PE
- PVC (Polyvinyl Chloride)
- PET (Polyethylene Terephthalate)
- Aluminum Foils
- Metallized Polyester
- Cellulose or Barrier Foils
It's noteworthy that heat sealing machines are typically not appropriate for use with cardboard boxes, indicating the need for different sealing approaches for such types of packaging.
What types of sealing machines are commonly utilized in the packaging sector?
What are Heat Sealers?
Heat Sealers are the most frequently used sealers in the packaging industry, serving a vital role across various sectors such as food, baking, parts and products. These devices employ heat to melt the packaging material, thereby forming a durable seal. Particularly effective for plastic bags and pouches, the most prevalent type of heat sealer is the impulse sealer. Impulse sealers apply a brief impulse of heat to close the bag and provide a durable seal. Distinguished by their energy efficiency, impulse sealers generate heat only when their sealing arm is activated, making them ideal for sealing thin plastic materials without harming the items inside.
The table below represents a detailed summary of the available sealing machines, highlighting their uses and features within the packaging sector.
Type of Sealer |
General Description |
Suitable Materials |
Special Features |
Foot Impulse Sealer |
Used for sealing plastic bags, allowing faster operation with hands-free. Suitable for moderate environments and larger width bags. |
Plastic bags |
Hands-free operation, suitable for larger bags. |
Constant Heat Sealer |
Seals foil, mylar, or poly cellophane bags with constant heat. Ideal for heavier bags and specialty items. |
Foil, mylar, poly cellophane bags |
Constant heat for heavier bags. |
Impulse Heat Sealer |
Suitable for entry-level, low volume packaging of poly bags and tubes. Works for most common bags. |
Poly bags and tubes |
Best for low volume, common bag sealing. |
Automatic Heat Sealer |
Rapid sealing of plastic bags with automatic heat sealing units. Good for larger width bags and higher production. |
Plastic bags |
Automatic operation for efficiency and larger bags. |
Impulse Sealer with Cutter |
For rapid sealing and cutting of roll bags, poly-tubing, and plastic materials. Provides durable seals. |
Roll bags, poly-tubing, plastic materials |
Seals and cuts for a durable seal. |
Vertical Impulse Heat Sealer |
Designed for vertical sealing of heavy bags or packaging of powders and liquids. Facilitates easy operation. |
Heavy duty bags, powders, and liquids |
Vertical sealing for operator ease. |
Double Impulse Sealer |
Ideal for heavy-duty applications requiring high temperatures. Can seal plastic lined, foil, and gusset bags. |
Plastic lined, foil, gusset bags |
High temperature sealing for heavy-duty applications. |
What are Cold Sealers?
Cold Sealing, utilizing only pressure, is favored for heat-sensitive items, particularly within the food industry, due to its gentle sealing process. This method involves a two-film system: one with reverse-printed branding and another providing a protective barrier. Once laminated, these films create a unified web, onto which cold seal adhesive is patterned to align with exterior graphics.
Selecting compatible films is crucial to avoid issues like blocking, where rolls cannot be unwound, or inadequate seals. The cold seal adhesive, a natural product, demands careful application due to its variability and potential for instability, necessitating expert knowledge for optimal use.
Improper handling can lead to significant waste and costs, and the risk of defective packaging reaching consumers, resulting in blocked rolls or inadequate seals. Therefore, premier packaging producers prioritize long production runs to minimize these risks.
The key advantage of cold-seal packaging lies in its speed, capable of outpacing heat-seal methods by up to tenfold, thereby delaying additional investments in packaging lines. This efficiency is achieved without the need for heat, simplifying the sealing process.
There are various types of cold sealing machines, including:
- Tabletop machines
- Mini cold sealing machines
- High-end machines
Selecting the appropriate cold sealing machine also hinges on the nature of the product being sealed, whether it's food or medicine.
Understanding Ultrasonic Sealers: what are they?
Ultrasonic Sealing utilizes high-frequency vibrations from a sealing tool to modify the structure of plastic at the molecular level. As plastic molecules vibrate, the material softens and bonds under pressure from a sealing anvil, creating a secure seal. This method is known for its efficiency and sustainability, offering several advantages:
- Reduced Packaging Waste: Achieves a focused seal area, minimizing the material needed per package and reducing overall packaging waste, leading to cost benefits in large production runs.
- Lower Energy Requirements: Without the need for heat, ultrasonic sealing consumes less energy and avoids the thermal energy emission typical of other methods, making it more energy-efficient.
- Enhanced Product Preservation: The absence of heat in the sealing process makes it suitable for temperature-sensitive items like frozen foods, chocolates, and pharmaceuticals, reducing spoilage.
- Minimal Maintenance: This process demands less mechanical intervention, leading to fewer replacements and lower maintenance costs.
- High-Quality Sealing: Ultrasonic sealing ensures airtight seals even in the presence of product residue, enhancing the integrity and shelf life of the package contents. It's equally effective for liquids and solids.
- Material Versatility: Capable of bonding a diverse range of materials due to its low operating temperature, ultrasonic sealing supports a wide array of packaging applications.
Ultrasonic sealing's investment pays off over time through savings in raw materials, energy, and maintenance. Its capacity for smaller, efficient seals reduces material use and waste. Additionally, its operational efficiency is reflected in various specialized sealing applications, including tube, pouch, and clamshell sealing, as well as automated processes like cross, back, and gusset sealing, zipper crushing, and fitment welding. This method offers a sustainable, versatile, and cost-effective solution for modern packaging needs.
What are Crimp Sealers, Jaw Sealers, Roller Sealers?
Crimp Sealers are specialized tools tailored for sealing individual pouches, available in both handheld and bench-mounted configurations. These devices are particularly effective for sealing polypropylene and foil bags, equipped with essential features such as safety and temperature controls for precision. Handheld crimp sealer models are designed to meet a variety of packaging requirements, capable of sealing small bags using impulse technology or managing curved or long items with roller sealers. Distinguished by their robust construction, these handheld units are suited for a range of materials including cellophane, foil, and heat-sealable labels. Their appeal lies in their lightweight design, ease of temperature adjustment, and the inclusion of an operational indicator light, making them user-friendly and efficient for packaging tasks.
Jaw Sealers, conversely, are built for larger-scale operations requiring extended sealing lengths and are typically set up on benches or floors. These sealers often incorporate footswitch activation for convenience and can be programmed to operate automatically, enabling continuous feed of packages into the seal bars without manual closure. Ideal for sealing polypropylene and foil bags, jaw sealers also feature safety and temperature controls, along with a foot pedal and clamps for stable and secure operation. The constant heat maintained in the jaws ensures reliable seals across a wide variety of package sizes and types, marking jaw sealers as essential equipment for intensive packaging environments.
Roller Sealers are portable roller heat sealers that are perfectly suited for sealing materials such as polyethylene or cellophane. Featuring a fabric-coated wheel, it effortlessly rolls over materials to form a durable seal. Capable of creating seals in various shapes including round, oval, or square textures, this device offers versatility with its unlimited sealing length and a variable temperature setting.
The Handheld Constant Heat Roller Sealer is designed for convenience, equipped with a heat-insulated handle, protective shield, and a stand to ensure safe usage. It's particularly effective for sealing aluminum bags and cellophane, utilizing a heated sealing rim wheel. Its manual operation is straightforward, making it highly portable and a cost-effective shipping choice due to its compact size. This sealer is an excellent tool for small businesses seeking an efficient sealing solution.
Understanding What are Pinch Bag Sealers and Capping Sealers.
Pinch Bag Sealers, crafted for sealing multi-layered paper and woven polypropylene bags, play a vital role in numerous packaging workflows. These machines come standard with a bag support conveyor, streamlining the sealing process. They can be further customized with coders for bag labeling, bag top trimmers for a polished look, and additional conveyors for enhanced bag handling and transportation.
The operation of pinch top bags centers around pre-applied hot melt adhesive on the bag openings. As these bags are fed through the pinch sealer, a blast of hot air melts the adhesive, facilitating the folding and neat closure of the bag's top. Subsequent compression ensures a tight seal, safeguarding the bag's contents. This method stands out for its effectiveness and reliability, offering a solid sealing solution for sectors in need of dependable packaging closures.
Capping Sealers are chosen based on cap size, shape, torque, closure style, container type, operating speed, space, and tamper-proofing needs. Induction sealing, a non-contact method, welds a foil laminate to container lips, enhancing tamper evidence—a method recognized by the FDA.
Induction Sealing Process:
- Power Supply and Sealing Head: The system consists of a power supply generating medium to high-frequency electrical currents and a sealing head housing an inductive coil. This setup creates an electromagnetic field.
- Sealing Mechanism: As containers pass under the sealer, the electromagnetic field heats the foil laminate, melting the polymer coating and bonding it to the container’s lip, achieving a hermetic seal.
Key Features:
- Induction Field Strength: Tailored to closure size and production speed, with sealing heads designed for specific applications. Flat heads cover large areas, while tunnel heads focus on caps for a uniform seal.
- Induction Liners: Various materials are available, including foam-backed and paper-backed foils, with customization options like logos for freshness seals. The liner's design, whether single or two-piece, affects seal integrity.
- Container Compatibility: Best suited for plastic containers with screw-on caps, though glass and metal can be sealed with additional considerations.
Selecting Induction Sealers:
Factors include cap size/type, line speed, container material, and product properties. Power level and sealing head design are crucial for efficient sealing, emphasizing energy transfer over kilowatt rating.
Understanding L-Bar Sealers and I-Bar Sealers?
L-Bar Sealers expertly encapsulate products, offering a precise seal particularly suited for shrink-wrap applications. These sealers are engineered specifically for wrapping with shrink film, allowing simultaneous cutting and sealing in a seamless operation. Operating an L-bar sealer is straightforward: simply adjust the timer, position the product within the fold of the shrink film, and lower the sealing arm. Gently withdraw the product post-seal; the sealing wire effectively trims and seals the film’s edge. Applying hot air via a heat gun or passing through a shrink tunnel then snugly conforms the film around the item, optimizing it for efficient shrink film packaging.
Constructed from steel, these sealers are built for robust, long-term use, demonstrating exceptional durability. Although the L-bar sealer itself focuses on sealing, leaving the shrinking process to a dedicated heat tunnel, this division of labor enhances operational efficiency, allowing continuous item processing without pause for shrinking. Operators manually place items into shrink wrap, then use a push-button to activate sealing under the L-bar. Designed with stainless steel, these sealers are perfect for environments that demand high levels of cleanliness, resist corrosion, and face moisture challenges. They feature an automatic sealing cycle, a closed-circuit cooling system for the sealing bars, and a coolant level monitor, ensuring operational efficacy. Compatible with both PVC and Polyolefin films, they boast low energy consumption and an intuitive control system for ease of use. L-bar sealers are available with heat gun systems too.
I-Bar Sealers are the perfect solution for small enterprises with modest packaging volumes, capable of efficiently handling up to 400 packages daily. These sealers excel in sealing and cutting shrink film, offering a cost-effective solution for achieving professional-grade packaging. With the ability to both shrink wrap and create bags from poly tubing, the I-bar system is versatile and requires no warm-up time due to its impulse sealing mechanism. Its robust build ensures long-lasting service, and it comes equipped with a convenient sliding cutter.
This system serves as an excellent entry-level kit for small businesses looking to package a wide range of products with a professional finish. It's advised to use shrink film rolls no wider than 16 inches, compatible with both PVC and Polyolefin films.
For operation, place the centerfold shrink roll on the film rack, ensuring the film weaves through the film separator; the top layer should rest above the separator with the bottom layer beneath it. This setup facilitates the creation of a pouch by sealing the film, where an initial seal forms the pouch, followed by two more seals per product to secure the packaging. This description outlines the seamless and efficient process of using an I-bar sealer for small-scale packaging needs, emphasizing its ease of use and versatility. I-bar sealers are available with heat gun systems too.
Below is the table summarizing the differences between L-bar and I-bar sealers based on the provided information:
Feature |
L-Bar Sealer |
I-Bar Sealer |
Sealing Process |
Seals all open ends of the shrink film in one step |
Requires rotating the product to seal all sides |
User Intervention |
No need to rotate the product |
User must rotate the product |
Speed |
Faster |
Slower |
Initial Cost |
More expensive |
Less expensive |
Long-term Cost Efficiency |
More cost-efficient for large orders |
Less cost-efficient for large orders |
Seal and Cut Operation |
Seal and cut simultaneously |
Requires two steps to seal and cut |
This table highlights the operational differences, cost implications, and efficiency aspects of L-bar sealers versus I-bar sealers, assisting in making an informed decision based on packaging needs and volume.
Understanding Band Sealers: What Are They?:
Band Sealers, also known as Belt Sealers, are perfectly suited for high-capacity packaging needs, sealing a vast array of thermoplastic materials including polyethylene, foil, plastic-lined, and gusseted bags, regardless of size or length. These sealers are designed for durability, with operating speeds adjustable to both lower and higher settings without causing wear. Each Rapid Sealer is equipped with an adaptable speed conveyor belt that can be adjusted in height or angle to suit various package sizes, effectively acting as an additional team member by significantly reducing packaging time.
Available in both horizontal and vertical orientations, band sealers offer versatility in direction, accommodating movement from right to left or vice versa. They come integrated with an inkjet printing system for real-time printing of barcodes, expiry dates, batch numbers, QR codes, custom texts, images, and unique symbols directly onto the packaging as it is sealed. This all-encompassing system maximizes the efficiency of inkjet printers, making it an invaluable tool for streamlining packaging processes.
Despite the larger size of band sealers contributing to higher freight costs, the investment pays off by markedly lowering production and labor expenses, making it a cost-effective solution for enhancing packaging operations.
Understanding Blister Pack Sealers, Clamshell Sealers, Tube Sealers.
Blister Packaging is a widely used packaging method, featuring a clear, form-fitting plastic cavity that is firmly bonded to a cardboard backing or film to encase and exhibit products securely. This form of packaging is prevalent across numerous sectors, with its most notable applications found in retail, medical, cosmetic, dental, electronics, consumer goods, office supplies, toys, sporting goods, and manufacturing industries.
Blister packaging offers several benefits including the preservation of freshness for food items through an airtight seal that guards against external elements like moisture, contamination, and physical damage. It enhances product visibility, boosts shelf appeal, allows for portion control, and provides tamper resistance, thereby ensuring the safety and integrity of the contents. Additionally, it serves as an effective means of product display and branding, offering customization options in terms of shape, size, and security features. Certain blister packs also include hook holes for convenient display, are designed to be eco-friendly, prolong the lifespan of consumable items, and can potentially drive sales increases due to the visibility of the product.
The selection of blister packaging sealers varies based on the specific requirements of the packaging, encompassing full face seals, trapped seals, partial face seals, blister trays, blister cards, and custom printed seals.The most commonly utilized blister packaging sealers include Full-face blister sealers, Partial-face blister sealers, Trapped blister sealers, Fold blister sealers, and Clamshell sealers.
Given that sealers tend to be substantial in size, shipping costs can be significant. Therefore, it's advisable to consult with manufacturers or distributors of sealers to discuss the specific product needing blister sealing, enabling them to provide the most suitable recommendations.
Clamshell Sealers are specialized tools designed for securely sealing clamshell packaging, effectively preventing product tampering or damage. These sealers are available in two main types: direct heat (constant heat) and ultrasonic. Direct heat sealers maintain a consistent temperature during operation, ensuring the clamshell is sealed through applied heat. In contrast, ultrasonic sealers use high-frequency vibrations to create a seal, remaining cool to the touch and offering a safer and faster sealing process, especially suited for higher production volumes.
Clamshell packaging, made from thermoformed plastic with a hinge, is ideal for enclosing and protecting products while allowing visibility and access prior to purchase. The choice between heat sealing and ultrasonic sealing depends on the specific needs of the operation and the material properties of the clamshell packaging itself.
It is recommended to test clamshell packaging beforehand as some, especially those with recycled content, may not seal effectively with these methods due to material inconsistencies. For clamshells that are challenging to seal with heat or ultrasonics, alternatives such as staples or clear adhesives may be employed.
Both handheld and automated clamshell sealers are available, with handheld models being particularly portable and cost-effective in terms of shipping. Whether for full-scale production or lower volume needs, selecting the appropriate clamshell sealer can significantly enhance packaging efficiency and product security.
Tube Sealers are used by dealers managing a variety of products from adhesives like super glue to daily essentials such as toothpaste, body lotions distributing these items in either plastic or metal tubes. These tubes, equipped with caps and with their other end open, are prepared for the filling process. The tube filling and sealing machine introduces a precise quantity of the product into each tube before sealing it. Options to imprint a batch number or expiration date on the seal are available if chosen. While metal tubes are sealed through a process of folding and crimping, thermoplastic tubes undergo a heat-sealing process followed by embossing. Sealers come in various forms, including ultrasonic tube sealers, semi-automatic, and fully automatic sealers. The initial step towards finding an appropriate solution for filling liquid or powdered products involves a clear understanding of the product's characteristics. Determining whether your product is of low viscosity, similar to water, or of a higher viscosity, akin to glue, is essential. This distinction is crucial in selecting suitable equipment, as it influences the choice of metering system, filling speed, and other aspects of the production process. It also plays a pivotal role in deciding whether a tube is an appropriate container for your product.
The question of how many tubes can be filled per production shift is paramount on the production side, impacting both production costs and timelines. The optimal solution might range from a manual handheld device, a semi-automatic machine, to a sophisticated, fully automatic line or even an automated rotary system, depending on the viscosity of the product, the type of tube, and the desired fill volume.
Understanding the specific fill volume necessary for your product is not as straightforward as it might seem, yet it's vital for identifying other related factors such as fill rate, product viscosity, and the appropriate metering systems. Different industries may have varying accuracy requirements for fill volumes to comply with certain standards, making it imperative to have a comprehensive understanding of the required fill volumes and industry regulations for successful production management.
Understanding Vacuum Sealers: What Are They?
Different Vacuum sealers are available in the market are as follows:
- Handheld Sealers: Compact, easy-to-use for small quantities. Limited capacity.
- Manual Sealers: Moderate sealing area, suitable for wet/dry goods, attachment-compatible.
- Nozzle Sealers: Simple, adaptable, beginner-friendly without special parts.
- Chamber Sealers: Large capacity, efficient for wet/dry items, higher cost.
Versatility & Usage
- Extends food shelf life.
- Supports marinating, sous vide cooking.
- Stores coffee beans, spices, baked goods.
Size & Selection
- Match sealer size with household size and sealing volume.
- Options from compact to larger models.
Key Selection Factors
- Automation: For ease of use.
- Optional Handheld Sealer: Adds versatility.
- Removable Drip Tray: Simplifies cleaning.
- Seal Only Feature: Allows for custom bag sizes.
- Included Accessories: Meets various needs.
Safety Considerations
- Be aware of potential suction injuries and burns, especially with handheld models.
Price & Lifespan
- Price Range: Budget-friendly manual devices to high-end models.
- Lifespan: 3 to 5 years, depending on usage, maintenance, material quality.
Impact on Sealing Process
- Handheld Models: Quick but less forceful.
- Chamber Sealers: Slower but more thorough.
Environmental Benefits
- Reduces packaging waste and food spoilage.
- Decreases landfill waste, promoting sustainability.
In conclusion, packaging sealers play an indispensable role in safeguarding products throughout their journey from manufacturer to consumer, particularly in the dynamic landscape of the United States market. By understanding the various types of sealers available, their functionalities, and the factors influencing their selection, businesses can ensure freshness, prevent contamination, and prolong shelf life. Investing in the right packaging material can significantly contribute to the success and integrity of your products in the competitive marketplace while ultimately enhancing brand reputation.
As technology continues to advance and consumer demands evolve, staying informed about the latest innovations and best practices in packaging sealing remains paramount for businesses aiming to thrive in the competitive marketplace. With a strategic approach to packaging sealers, businesses can effectively mitigate risks, minimize waste, and maximize the longevity and quality of their products, ultimately contributing to a more sustainable and resilient supply chain ecosystem. So, take the time to evaluate your packaging needs, explore the options available, and embark on a journey towards optimized product protection with the right packaging solution tailored to your business requirements.