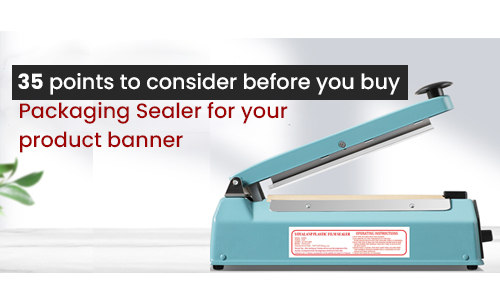
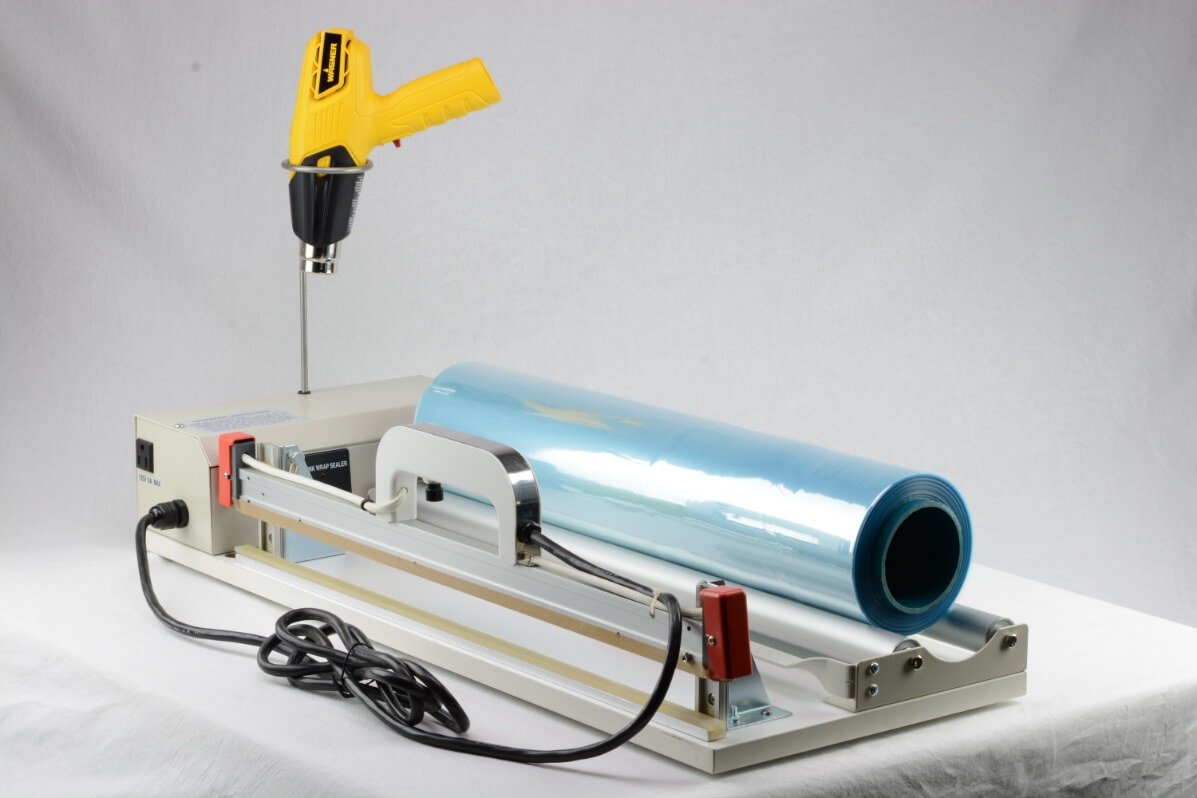
35 Points to Consider Before You Buy a Packaging Sealer for Your Product
- Type of Sealer: There are several types of sealers from size to its capabilities. The most common ones that are used by small companies are as below:
-
- Foot Operated Sealer: Standard, Standard with Trimmer, Double Impulse Upper Jaw, Double Impulse Seal and Trim, Adjustable Angle, Double Impulse Vertical, Vertical Continuous Heat Stainless Steel, Continuous Heat, Continuous Heat Double, Pneumatic Impulse, Pneumatic Continuous Heat.
- Tabletop Heavy Duty Sealers: Semi-automatic Heavy Duty Impulse, Semi-automatic Upper Jaw Impulse, Semi-automatic Double Impulse, Semi-automatic Continuous, Stainless Steel Temperature Precision Automatic with Trimmer, Temperature Precision Impulse Automatic.
- Vacuum Sealers: Original Standard, Gas Flush, Double Seal, Gas Flush with Temperature Adjustment, Compressor-less Sealers.
- Shrink Wrap Sealers: I Bar, L Bar, I Bar Portable, I Bar Hybrid, Shrink Tunnel.
- Band Sealers: Stainless Steel, Tabletop Portable, Heavy Duty Industrial Vertical, Left to Right Printer, Right to Left Printer, Vertical with Dry Ink Printer, Vertical with Dry Ink Printer and Gas Flush, Vertical with Dry Ink Printer and Vacuum, Vertical with Dry Ink Printer with Vacuum and Gas Flush.
- Separate Imprinters can be bought as attachments, it can be Manual, Continuous, Impulse and Foot Operated.
- Stainless Steel Food Film Wrappers are also available which are FDA approved to Wrap food.
- Here's a table to understand the terminology used in Sealers:
Sealer Type
Description
Tabletop
Can be kept on table for operation.
Manual
Hand operated.
Standard
Regular size.
XL
Extra large.
Trimmer
Acts as a cutter.
Heavy Duty
Strong, can seal materials up to 20 mm thick.
Portable
Movable.
Magnetic
Has a sealer magnet that holds down the sealing arm and automatically releases after the cooling cycle.
Double Impulse
Utilizes twin heating element wires on the top and bottom of the sealing jaw.
Double Impulse Seal and Trim
Designed to cut and seal in one operation.
Adjustable Angle
The head can convert from a horizontal to a vertical sealer.
Double Impulse Vertical
Utilizes twin heating element wires vertically for sealing powders and liquids.
Continuous
Provides continuous heat on its upper jaw for mesh seals.
Pneumatic
Offers strong, consistent, and controllable sealing pressure.
Semi-automatic
Features a timer-controlled electromagnet that pulls the sealing arm down for an even pressured seal.
Upper Jaw
Only the upper jaw of the sealer is heated.
Automatic
Includes an emergency shut-off switch to prevent injury during operation.
Temperature Precision
Requires verification of seal temperatures on impulse sealers.
Gas Flush
Removes oxygen and moisture from the bag needing sealing.
Double Seal
Can seal 2 bags at the same time.
Temperature Adjustment
Allows temperature to be adjusted to the desired level.
Compressor-less
Contains an internal air compressor; no need for an external connection.
Vacuum
Creates a vacuum inside the bag; no air inside.
I-Bar
Seals on only one side of the products at one time.
Hybrid
Combination of both I-Bar Sealer and Portable.
L-Bar
Seals both vertically and horizontally at the same time, saving time.
Shrink Tunnel
Features an adjustable speed conveyor and separate temperature controllers for upper and lower heaters.
Left to Right Printer
Prints from left to right.
Right to Left Printer
Prints from right to left.
Sealer with Dry Ink Printer
Capable of printing 20-40 characters at one time.
- Material Compatibility: Choose a sealer that can handle the specific materials you need to seal, such as film, shrink wrap, poly bags, poly tubing, aluminum foil, bottles, and paper.
- Thickness of Material: Ensure the sealer can handle the thickness of the material you plan to seal. Sealers usually provide the max thickness of the material it can seal. For example, if the sealer has a sealing strength of 12 Mil poly bag, it can still seal 6 Mil poly bag, by adjusting temperature, time and pressure of the sealer but it cannot seal a 24 Mil polybag.
- Cost: Factor in the initial purchase price and any ongoing costs related to maintenance and supplies of the sealer. Sealers that are expensive should be tested onsite before purchasing it. As after purchase if needed to return the sealer the return shipping cost would incur an extra expense.
- Quantity of Products: Consider whether the sealer is appropriate for sealing small or large quantities of products. This affects the type and size of the sealer you will choose. This will also help to decide if you want to buy automatic, semi-automatic or manual sealers.
- Quality Of the Seal: To make sure the quality of the seal of the product that the sealer provides is not compromised at any point. To make sure the seal is leak- proof as well to avoid the contamination through air, bugs, or any other outside external elements.
- Sealing Speed: Determine the speed at which the sealer operates, which is crucial for meeting production demands. Sealing speed also affects the labor cost involved. Manual sealers with huge quantities would incur higher labor costs and more production time.
- Compliance and Approval: Check if the sealer is suitable for food or medical packaging and whether it complies with Health Department Regulations and FDA approvals.
- Size, Weight and Space Requirements: Consider the dimensions and weight of the sealer to ensure it fits in your designated area and is manageable. Assess the amount of space you have available for the sealer and whether it can be adjusted to fit into your working environment.
- Tamper Resistance: Determine if the sealer provides tamper-resistant sealing if required for security or safety standards. Tamper resistance seal can reduce the loss in the company
- Type of Heating Plates: Decide between flat, round, vertical, horizontal, custom heating plates based on your needs.
- Cutter (Trimmer): Consider whether you need a sealer with a built-in cutter for ease of use. Sealers with cutters can have the benefit of sealing custom size bags from films. Sealers are available with a cutter and without a cutter. Sealers without cutters are cheaper in cost.
- Heat Sealer Dwell Time: Heat Sealer Dwell Time means time required when the heating elements in sealers come in contact with the packaging material, and it is allowing them to form a bond/seal. The sealer may have only upper jaw heating, only lower jaw heating or both upper and lower jaw heating. Correct temperature and pressure can determine the right Dwell Time.
- Sealer Switch Type: To make sure what is more comfortable in operation of the sealer is its Foot Switch or Hand Switch or Press.
- Sealing Pressure: Sealing pressure determines the seal strength of the material. To have the right amount of seal pressure can impact seal quality. Temperature and time also are co-related to sealing pressure. It's important to have the right sealing pressure.
- Sealer Tests: The product sealed by a specific sealer may undergo several tests to assess the quality standard that the sealer delivers when sealing a product.
- Seal Strength Test (ASTMF88)
- Burst Strength Test (unrestrained) (ASTMF1140)
- Visual Inspection Test (ASTMF1886)
- Burst Strength Test (restrained) (ASTMF2054)
- Hot Tack Test (ASTMF1921)
- Portability: Assess whether the sealer needs to be portable and whether its weight affects portability. Sealers which are light weight can easily be moved from one place to another, when required. Table top sealers are easy to move and they are also lightweight.
- Construction Material: Choose a sealer made from materials that suit your needs, such as Plastic, Stainless Steel, or Other Metals.
- Operation Mode: Decide between a Manual, Semi-automatic, Automatic sealer based on your operational preference.
- Additional Features: Consider if the sealer offers Printing capabilities, Lamination, or both, Sealing Pattern.
- Reliability and Maintenance: Evaluate the reliability of the sealer and how frequently it needs maintenance and calibration.
- Warm-up and Cooling Times: Check the warm-up and cooling times to see if they align with your operational needs.
- Gas Purge Option: For Vacuum sealing, determine if a Gas Purge feature is necessary to remove oxygen and moisture.
- Safety Features: Ensure the sealer has adequate Safety Features to protect operators.
- Ease of Use: Evaluate how user-friendly the sealer is.
- Electrical Requirements: Make sure the electrical requirements of the sealer match what you can provide.
- Temperature Control: Check if the sealer has a Digital Temperature Controller for precise operations.
- Certifications: Look for any relevant Certifications that endorse the sealer’s quality and safety. Some sealers may have below certifications:
- Fair Packaging And labeling Act (FPLA)
- Poison Prevention Packaging Act (PPPA)
- Certificate of Compliance from Manufacturers and Importers
- American Society of Testing and Materials (ASTM)
- International Safe Transit Associations (ISTA)
- Food and Drug Administration (FDA)
- Underwriters Laboratory Certified ( UL)
- Variable Time Controller: Check if the sealer has a Variable Time Controller, which allows you to adjust the sealing time based on the type of material and the seal strength required.
- Long Lasting Seal: Ensure that the sealer is capable of creating long-lasting seals that are durable and resistant to wear and tear, ensuring the integrity of the package.
- Energy Efficiency: Consider the energy consumption of the sealer. An energy-efficient model can reduce operational costs and is better for the environment.
- After-Sales Support: Look into the level of after-sales support provided, including availability of spare parts, customer service, and technical assistance from the company sealer is bought. Good support can significantly extend the lifespan and effectiveness of the sealer.
- Parts Availability: Choose a sealer with easily accessible parts to simplify repairs and reduce costs, extending the sealer's lifespan and efficiency.
- Service Kits and Return Policy: Consider if the sealer comes with service kits and whether it is returnable if it doesn’t meet your expectations.
- Shipping Costs: Include shipping fees in your budget, as they can vary based on the sealer’s size, weight, and shipping distance.