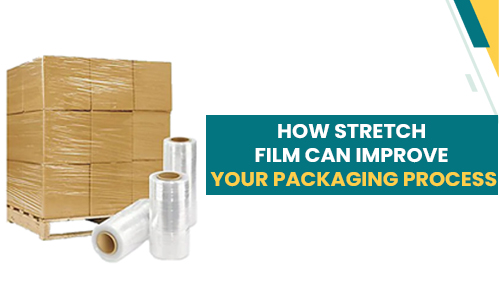
How Stretch Film Can Improve Your Packaging Process
In numerous warehouse and business operations, stretch film serves as an extensively utilized product on a daily basis. Its primary role involves ensuring the security of most pallets during storage and transit, resulting in a significant accumulation of stretch film usage, estimated at around 150,000 tonnes per year.
Frequently, businesses tend to assess their stretch film purchases solely based on the cost of individual rolls. However, the actual expenses related to stretch film predominantly hinge on the amount of material used to film each pallet. If your operation hasn't yet undergone an assessment of its stretch wrapping process, there exists a substantial potential for considerable savings. To pinpoint areas where costs can be reduced, it's essential to initially explore the various stretch film options available and determine which aligns best with your specific needs.
This article delves into all the essential aspects concerning stretch wrap, empowering you to make an informed decision and choose the optimal product for your business.
What is Stretch Film:
Stretch wrap, a thin and flexible plastic film usually crafted from polyethylene, serves the purpose of fastening and securing cased goods onto a pallet. During the wrapping process around the pallet, the application of tension allows the film to expand its length by as much as 300%.
Since its inception in the packaging industry during the early 1970s, Stretch Film has undergone significant evolution. Within this period, it has experienced three major transformations, marking its development in the industry. The initial introduction of the first two types of stretch film dates back to around 1972.
Stretch Film Material:
The production of this film involves molten resin being directed through a substantial extruder, exerting pressure to create a thin film layer over a sizable drum, subsequently cooled. Once cooled, this plastic layer is cut and wound into rolls of stretch film. The prevalent material for stretch film is LLDPE (Linear low-density polyethylene), formed through the copolymerization of ethylene with alpha-olefins. Among these, butene, hexene, and octene are the most commonly used.
Gauging the Best Stretch Wrap Thickness
Gauge serves as the measurement of the wrap's thickness, which can differ based on its intended use. As a general rule, the higher the gauge, the greater its resilience against breakage.
25-30 GA: Pre-stretched film functions akin to standard gauge films, designed for loads of up to 2,400 lbs.
35-39 GA: Pre-stretched film performs comparably to standard and heavier-duty gauge films, suitable for loads reaching 4,000 lbs. This variant is sturdier, tighter, with reduced stretch, effectively handling loads up to 1,800 lbs.
37-42 GA: Employing high-performance film technology, this type matches the strength of standard 60 – 70 gauge films, adept at handling loads of up to 2,000 lbs.
47-55 GA: Utilizing high-performance film technology, this kind matches the strength of standard 70 - 80 gauge films, accommodating loads of up to 2,500 lbs.
61-65 GA: Employing high-performance film technology, this type matches the strength of standard 80 – 90 gauge films, suitable for loads up to 3,000 lbs.
75 GA: Utilizing high-performance film technology, this film matches the strength of standard 90 - 120 gauge films, handling loads up to 4,000 lbs.
50-60 GA: Intended as general-purpose light-duty gauge films, suitable for loads up to 1,600 lbs.
70-90 GA: Designed as general-purpose standard-duty gauge films, suitable for loads up to 3,000 lbs.
120 GA+: Tailored as general-purpose heavy-duty gauge films, ideal for loads up to 4,000 lbs.
Types of Stretch Film Rolls:
The primary varieties of stretch film rolls include hand stretch film and machine stretch film. Hand stretch film entails manual application by hand and is typically utilized for low-volume packaging purposes. On the other hand, machine stretch films find their use in high-volume packaging applications and are applied using machines.
Designed specifically for employment with a stretch wrapping machine, machine stretch film offers several advantages. It is faster to apply compared to hand stretch film, comes at a lower cost, enhances safety, and delivers superior load containment.
Types of Stretch Wrap:
When you consider purchasing stretch wrap, the initial step involves identifying the specific type of film that aligns with your operation's requirements. If your warehouse entails various wrapping tasks, opting for a general-purpose film might be the appropriate choice. For handling electronics, the ideal selection would be anti-static wrap. In the case of storing and shipping highly important or valuable goods, opting for high-performance stretch film ensures the desired level of performance.
The key takeaway is that there exists a type of stretch film tailored to meet your specific needs. It's a matter of assessing your requirements and then selecting the appropriate stretch film that fulfills those needs accordingly.
- General Purpose: Available in 50-120 gauge films for both hand and machine grades, this versatile film suits most applications, offering a range of gauges suitable for diverse tasks.
- High-Performance: Ranging from 37-75 gauge films for both hand and machine grades, these newer technology films provide heightened strength and puncture resistance at thinner gauges compared to general-purpose wraps.
- Anti-static: Offered in 80 gauge films for both hand and machine grades, this film is designed to shield electrical goods during shipment from static discharge.
- Pre-stretched: Available in 25-39 gauge films for hand grade only, this type provides consistent wrapping tension, ensures good load stability, and is lighter for easier handling compared to higher-gauge wraps.
- Color Coding: Available in 80 gauge films for hand grade only, this film is utilized to indicate how contents should be handled, shipped, or stored, aiding in organization and logistics.
- Breathable: Provided in 80 gauge films for hand grade only, this netted or vented film allows air circulation around the product, typically used for shipping produce or items requiring refrigeration.
- Product Concealing: Offered in 80 gauge (20.3 Micron) films for both hand and machine grades, this film protects privacy and aids in theft prevention by concealing the contents effectively.
Each type of stretch film serves distinct purposes and is tailored to specific requirements, ensuring efficient and appropriate packaging for various goods and applications.
Blown Stretch Film vs Cast Stretch Film:
Cast Stretch Films:
- Manufacturing Process: Produced via the cast extrusion process.
- Transparency: Exhibits excellent transparency, providing clear visibility of packaged items.
- Barrier Properties: Offers a remarkable barrier against aromas, moisture, and gases, ensuring better protection for the goods.
- Uniform Thickness: Maintains a consistent and uniform thickness throughout the film.
- Thickness Flexibility: No limitations on film thickness, allowing for versatility in choosing specific thicknesses.
Blown Stretch Films:
- Manufacturing Process: Created through the blown film extrusion process.
- Durability: Known for enhanced durability, providing maximum toughness in comparison to cast stretch films.
- Puncture Resistance: Offers superior puncture resistance, ensuring added protection for packaged goods.
- Reduced Manufacturing Scrap: Produces less manufacturing scrap during the production process.
- High Cling: Exhibits a high level of cling, facilitating better adherence to items being wrapped.
Each manufacturing process and resulting film type—cast or blown—comes with its own set of attributes and advantages, catering to different packaging needs and preferences based on factors such as transparency, toughness, puncture resistance, and manufacturing efficiency.
Tips for choosing the Right Stretch Wrap
Selecting the appropriate stretch film for your company involves several key considerations:
Load Weight: The strength of the stretch film gauge should align with the weight of the load. Heavier loads necessitate a stronger gauge for adequate support.
Load Shape: The nature of the load matters; uniform loads like same-size boxes on pallets require less holding power and a lower gauge. Irregular or unstable loads with sharp edges demand higher gauge and durability.
Tools and Training: Assess if your staff has the necessary tools and training. For large, heavy, or irregularly shaped items requiring high-gauge wrap, stretch-wrapping machines might be essential for safe and efficient wrapping. Proper training is vital to maximize machine benefits and prevent workplace incidents.
Special Product Needs: Consider if your products have specific requirements. Some items, like electronics, might benefit from anti-static wraps, while more valuable products might require opaque wraps for added concealment.
Stretch Wrapping Machine: Evaluate your shipping volume, staff size, and product types to determine if investing in a stretch wrapping machine is advantageous. Machines offer efficient and uniform tension application, particularly beneficial for large, bulky, or irregularly shaped products.
Choosing the right stretch film entails careful consideration and is not without its risks. If you're uncertain, have queries, or face a dilemma between options, feel free to reach out. At UCanWrap, we prioritize our customers' needs and aim to provide the best solutions tailored to your company's requirements.